Category | Parameter | Value/Details |
---|
Chemical Composition | Nickel (Ni) | ~65% |
| Molybdenum (Mo) | 28-30% |
| Iron (Fe) | 1-3% |
| Chromium (Cr) | 1-3% |
| Cobalt (Co) | 2-3% |
| Tungsten (W) | ≤ 3% |
| Manganese (Mn) | ≤ 3% |
| Silicon (Si) | ≤ 0.1% |
| Carbon (C) | ≤ 0.01% |
Physical Properties | Density | 9.22 g/cm³ |
| Melting Point | 1370-1418°C (2500-2585°F) |
Mechanical Properties | Tensile Strength | 758 MPa (110,000 psi) |
| Yield Strength | 352 MPa (51,000 psi) |
| Elongation (in 2 inches) | 40% |
| Hardness | 85 HRB |
Corrosion Resistance | Primary Resistance | Excellent in hydrochloric, sulfuric, acetic, and phosphoric acids |
| Oxidizing Resistance | Limited resistance to oxidizing environments |
| Localized Corrosion Resistance | High resistance to pitting and stress corrosion cracking |
Thermal Properties | Maximum Service Temperature | ~870°C (1600°F) |
Fabrication | Weldability | Good, with minimal risk of forming harmful phases during welding |
| Machinability | Comparable to other nickel-based alloys |
Applications | Typical Uses | Chemical processing, energy production, pollution control, pharmaceutical production |
Key Features of Hastelloy B3 Alloy Strips
Exceptional Corrosion Resistance: Hastelloy B3 alloy strips are known for their outstanding resistance to hydrochloric acid at all concentrations and temperatures. They are also resistant to sulfuric, acetic, formic, and phosphoric acids, making them suitable for chemical processing industries. The alloy’s resistance to reducing environments helps protect equipment from corrosion-related damage, extending service life.
Enhanced Thermal Stability: Hastelloy B3 exhibits better thermal stability than previous generations of Hastelloy B alloys. This stability makes it less prone to the formation of unwanted phases during heat treatment or welding, which can otherwise lead to embrittlement and loss of corrosion resistance.
Localized Corrosion Resistance: One of the notable improvements in Hastelloy B3 is its increased resistance to pitting and stress corrosion cracking. These forms of localized corrosion can severely compromise materials in aggressive environments, making the enhanced protection of Hastelloy B3 a significant advantage in applications where reliability is crucial.
Fabrication and Welding Characteristics: Hastelloy B3 can be readily fabricated using standard methods. Its improved welding characteristics allow for easier joining without compromising the material's structural integrity or corrosion resistance. The alloy can be formed into strips, sheets, plates, and other shapes, offering flexibility in design and manufacturing processes.
Applications of Hastelloy B3 Alloy Strips
Due to its exceptional performance in corrosive environments, Hastelloy B3 alloy strips are widely used in industries such as:
Chemical Processing: Equipment exposed to harsh chemicals, including reactors, heat exchangers, and piping systems, benefit from the corrosion resistance and durability of Hastelloy B3 alloy strips.
Pharmaceutical Production: In environments where purity and resistance to contamination are critical, Hastelloy B3’s corrosion resistance helps maintain the integrity of production equipment.
Energy Production: Hastelloy B3 alloy strips are utilized in geothermal, nuclear, and petrochemical plants where materials are exposed to extreme temperatures and corrosive gases.
Pollution Control: The alloy’s ability to withstand corrosive waste streams makes it valuable in scrubbers, ducts, and other components of air pollution control systems.
Hastelloy B3 alloy strips represent a significant advancement in the development of nickel-based alloys for use in highly corrosive environments. With superior corrosion resistance, enhanced thermal stability, and excellent fabricability, this alloy is a preferred choice for industries that require reliable performance under severe conditions. Whether in chemical processing, energy production, or pollution control, Hastelloy B3 alloy strips ensure long-term durability and protection against the most aggressive chemical exposures.
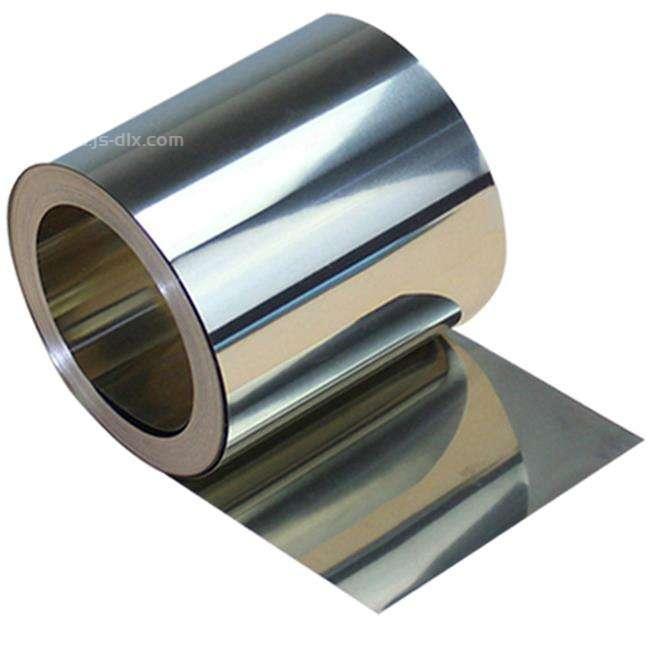
Why Hastelloy B3 Alloy Strip Is Not Widely Used As Hastelloy C276 Strips?
Hastelloy B3 and Hastelloy C276 are both high-performance nickel-based alloys, but they are designed for different environments and have different performance characteristics. Hastelloy B3 is specifically formulated for reducing environments, particularly where hydrochloric acid and other strong reducing acids are present, while Hastelloy C276 is known for its broad resistance to both oxidizing and reducing environments.
The reason Hastelloy B3 alloy strips are not as widely used as Hastelloy C276 strips can be attributed to several key factors:
1. Versatility
Hastelloy C276: This alloy offers excellent resistance to a wide variety of corrosive environments, including both oxidizing and reducing conditions. It performs well in settings that involve exposure to chlorides, sulfuric acid, phosphoric acid, acetic acid, and more. This versatility makes it a popular choice across multiple industries, including chemical processing, power generation, pollution control, and marine environments.
Hastelloy B3: While it excels in reducing environments, such as those involving hydrochloric acid, it does not offer the same level of protection in oxidizing environments. This limits its application to more specialized uses where the environment is predominantly reducing.
2. Resistance to Oxidizing Conditions
Hastelloy C276: One of its key strengths is its resistance to oxidizing environments, including nitric acid and ferric and cupric salts, which can be highly corrosive. This broad resistance makes it suitable for more general applications in environments that may involve a mix of oxidizing and reducing conditions.
Hastelloy B3: Although it has excellent resistance to reducing acids, its performance in oxidizing conditions is less reliable. This makes it less suitable for applications where exposure to both oxidizing and reducing agents is expected.
3. Market Demand and Availability
Hastelloy C276: Because of its broad applicability, Hastelloy C276 is more widely produced and stocked by suppliers. This availability translates into better pricing, quicker lead times, and easier sourcing for manufacturers. As a result, industries that require high-performance materials often default to C276, knowing it will likely meet their needs across a variety of scenarios.
Hastelloy B3: Its more specialized nature means that the demand is lower, leading to less frequent production runs and lower inventory levels. This can result in longer lead times and higher costs, making it less attractive for applications where C276 can also be used.
4. Cost Considerations
Hastelloy C276: Although both alloys are expensive due to their high nickel and molybdenum content, the widespread use of C276 helps mitigate costs through economies of scale. Additionally, because it can be used in a broader range of applications, companies may prefer to standardize on C276 rather than stock multiple alloys for different environments.
Hastelloy B3: Its specialized nature and lower demand often result in higher costs, both in terms of raw material and processing. For companies that don’t need the specific benefits of B3 in reducing environments, C276 offers a more economical solution.
5. Performance in Specific Applications
Hastelloy C276: Its ability to perform well in a wide range of aggressive chemicals, including both oxidizing and reducing acids, makes it a more general-purpose material. It is commonly used in environments where the exact nature of the corrosive agents may vary, and thus provides a safer option for engineers seeking a material that will work across different conditions.
Hastelloy B3: In applications where the environment is exclusively reducing (e.g., concentrated hydrochloric acid), Hastelloy B3 might outperform C276. However, since many industrial environments contain a mix of reducing and oxidizing conditions, C276 tends to be the more reliable choice.
While Hastelloy B3 is an excellent alloy for specific, highly corrosive reducing environments, its lack of versatility compared to Hastelloy C276 limits its widespread use. Hastelloy C276’s broad applicability, market availability, and resistance to both reducing and oxidizing conditions make it a more commonly used material in various industries. For applications that require handling multiple types of corrosive agents, C276 is often the preferred choice, leading to its more frequent usage compared to the more specialized Hastelloy B3 alloy strips.
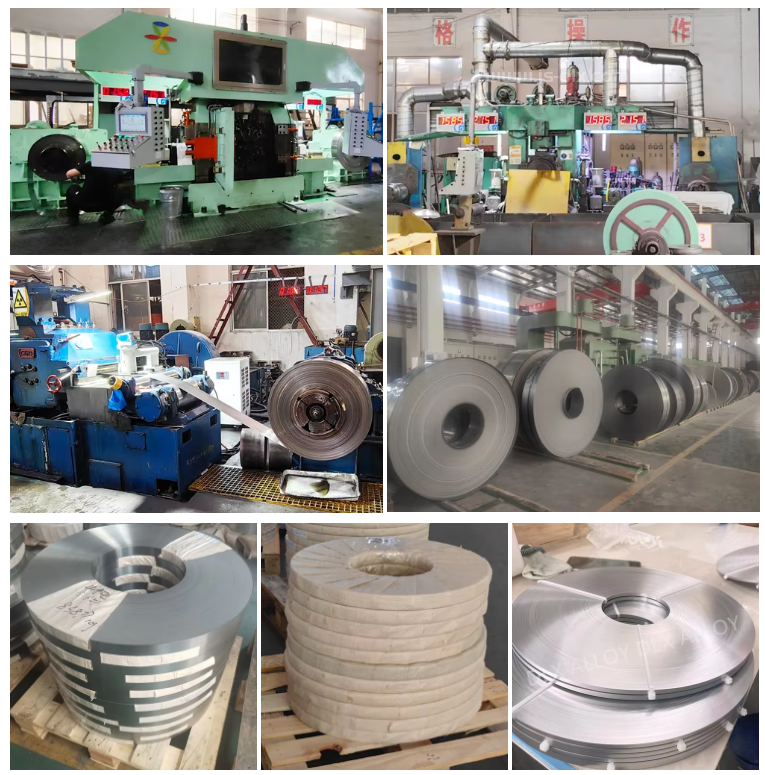
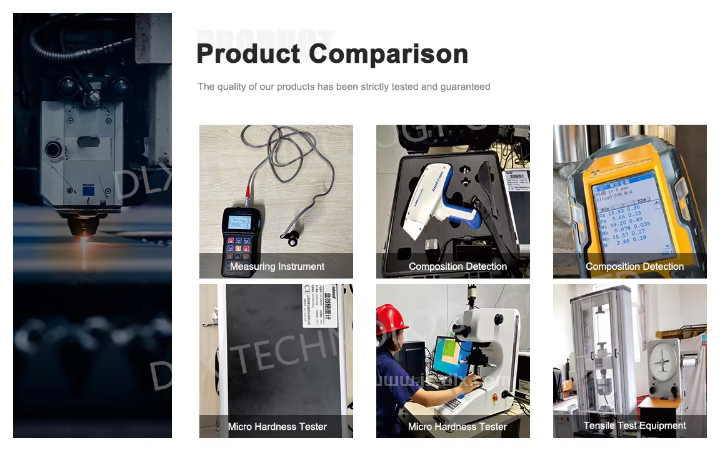
OEM Services:We offer personalized customization services for both products and labels to meet the specific needs of our customers. We can provide products with different thicknesses and widths according to the customer's requirements. Whatever kind of customization service our customers need, we will do our best to meet their demands and ensure customer satisfaction.
Company Profile:
DLX Alloy is a company dedicated to the production and research and development of alloys. Founded in 2002, we initially focused on the production of resistance alloys. Over the past 20 years, we have continued to conduct research and development and now offer a range of alloy products, including Inconel, Monel, Hastelloy, high-temperature alloys, and other nickel-based alloys. Our commitment to meeting the needs of industries that require high strength, strong corrosion resistance, and high-temperature performance is reflected in our focus on developing these alloys.
FAQ:
What is your working time?
Monday-Saturday : 7:30AM-17:00PM (Beijing time, GMT+08.00)
We have public holiday during May.1-3, Oct.1-7 and Chinese New Year holiday . Pls email us during our holiday if u have any question.
Do you provide free samples?
Yes, we can provide a free sample for testing,buyer should bear all the shipping costs.
What is your payment terms?
T/T,L/C,D/A,D/P,Western Union,MoneyGram,Paypal
What is the lead time of sample order?
Usually sample lead time is 7-15 days after payment has been confirmed.